Difference between bucket elevators
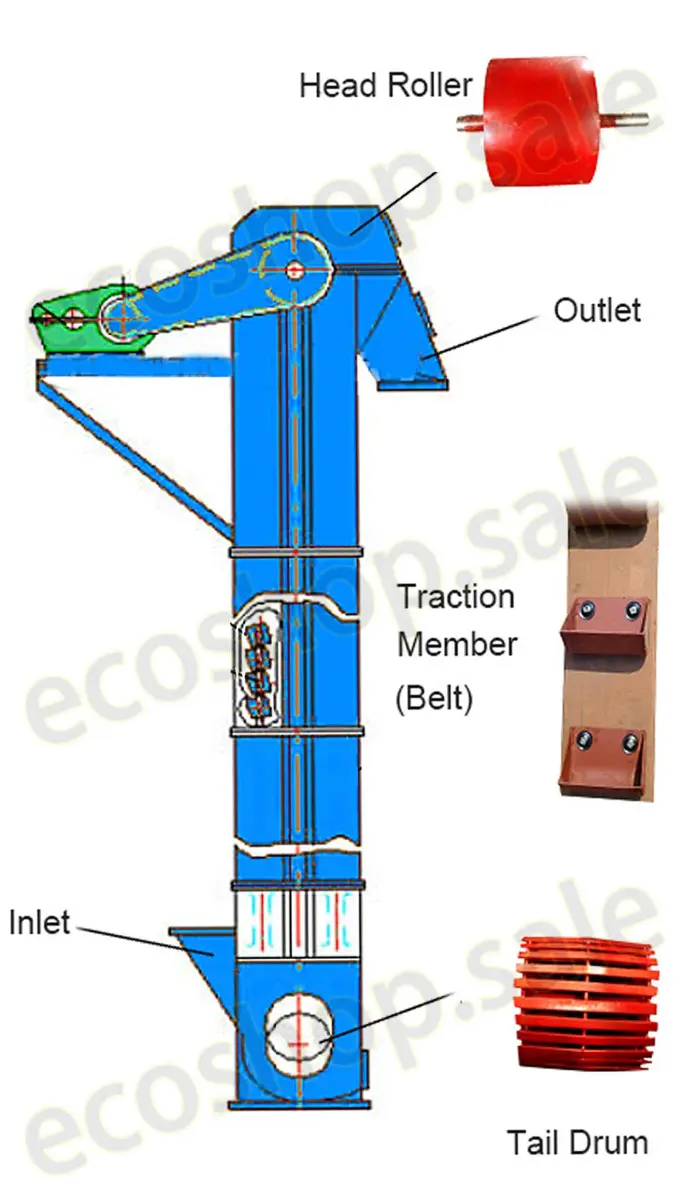
TDG Series
Steel Cord Belt Bucket Elevator--The traction part is steel cord core conveyor belt, adopting centrifugal or mixing method of discharging, which is suitable for conveying non-abrasive and semi-abrasive materials in the form of powder, granule and small block with the accumulation density less than 1.5t/m3. When ordinary rubber belt is used, the material temperature should not exceed 60℃; when heat-resistant rubber belt is used, the maximum material temperature should not exceed 150℃.
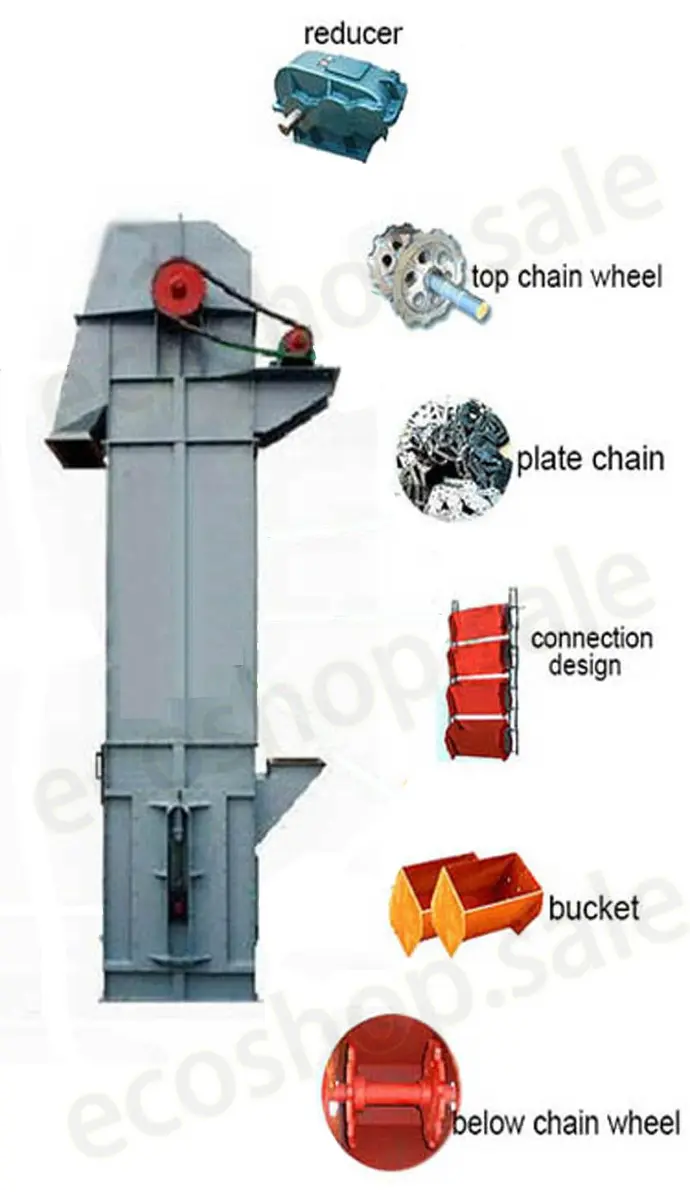
TH Series
Round Chain Bucket Elevator--The traction parts are high-strength round ring chain, adopting mixed type or gravity type discharging, suitable for conveying non-abrasive and semi-abrasive materials of powder, granule and small block with the bulk density less than 1.5 t/m3, and the temperature of the materials should not be more than 250°C. The bucket elevator can be used for conveying powder, granule and small block, and the temperature of the materials should not be more than 250°C.
View the product
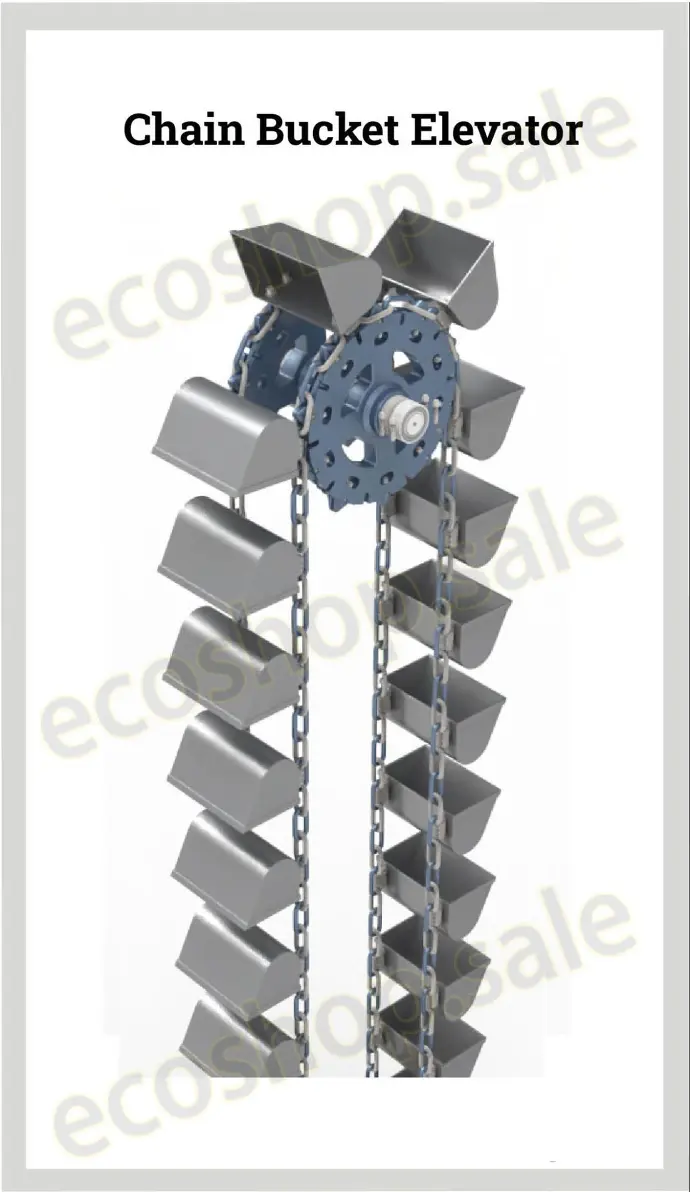
NE Series
Plate Chain Bucket Elevator--The traction part is plate sleeve roller chain, the running speed of the hopper is 0.5 m/s, and it adopts gravity type discharging method, which is suitable for conveying the medium and large lumpy abrasive materials with the stacking density of less than 2.2t/m3, and the temperature of the materials should not be more than 250°C. The bucket elevator is designed to be used for the transportation of the materials of the same size, which is suitable for the transportation of the materials with the density of less than 2.2t/m3.
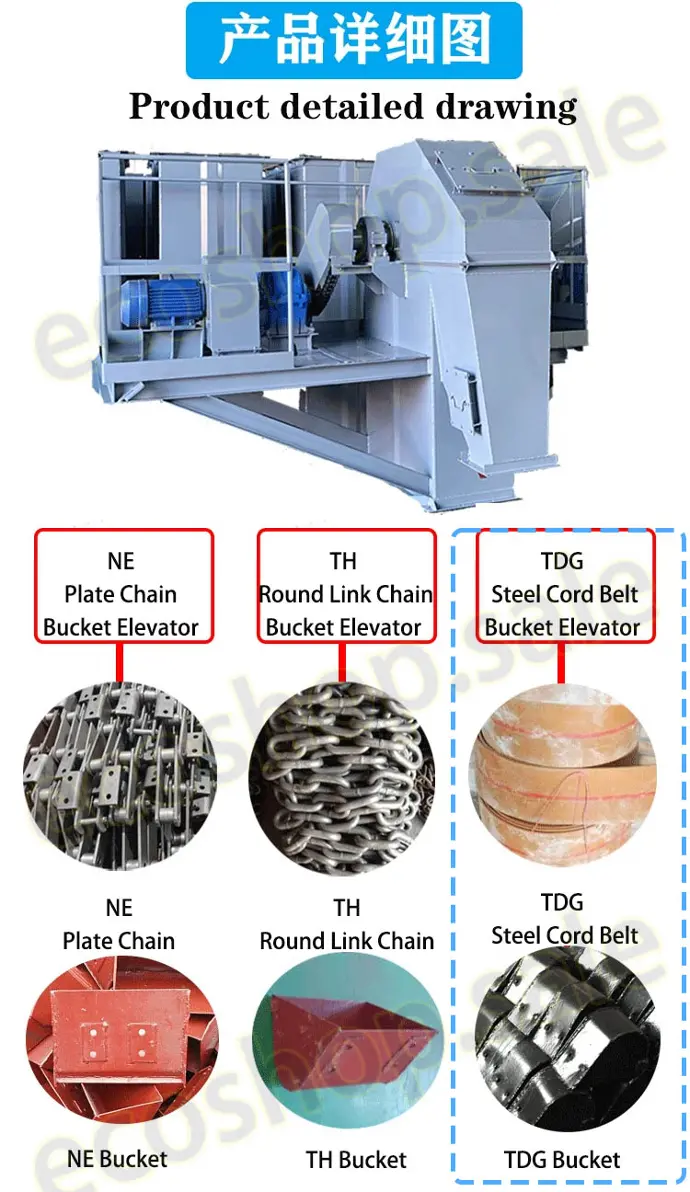
Comparison
In summary, bucket elevators utilizing steel cord belts excel in handling light, non-abrasive materials at lower temperatures, making them ideal for food and chemical industries. Ring chain bucket elevators, capable of withstanding higher temperatures, are suited for transporting moderately dense materials in sectors like metallurgy and construction. Plate bushed roller chain bucket elevators, designed for heavier, abrasive materials at elevated temperatures, find their application predominantly in mining and heavy manufacturing. Each type is optimized for specific material characteristics and industry demands, ensuring efficient vertical transportation in diverse industrial settings.